Introduction
Imagine a world where metal fabrication shops can predict machine failures before they happen, optimize production schedules in real-time, and minimize waste like never before. Sounds like science fiction? Thanks to the Internet of Things (IoT), this is now a reality. IoT applications in the metal fabrication industry are revolutionizing the way manufacturers operate, providing predictive insights that enhance efficiency, reduce downtime, and improve overall productivity.
What is IoT in Metal Fabrication?
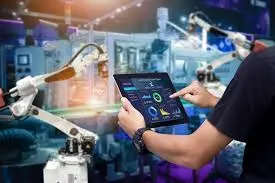
The Internet of Things (IoT) refers to a network of interconnected devices that collect and share data. In metal fabrication, IoT devices are embedded in machines, tools, and production lines to monitor performance, detect issues, and provide actionable insights.
The Role of Predictive Insights in Metal Fabrication
Predictive insights involve using IoT-generated data to anticipate and address potential problems before they cause disruptions. By leveraging sensors, data analytics, and artificial intelligence (AI), manufacturers can forecast maintenance needs, optimize workflows, and enhance quality control.
Benefits of IoT in Metal Fabrication
1. Reduced Downtime
IoT-powered predictive maintenance helps prevent unexpected machine breakdowns by identifying wear and tear in advance. This proactive approach significantly reduces downtime and extends equipment lifespan.
2. Enhanced Operational Efficiency
With real-time monitoring, manufacturers can optimize energy consumption, adjust production schedules, and eliminate bottlenecks, leading to increased efficiency.
3. Cost Savings
By reducing maintenance costs, minimizing material waste, and improving process efficiency, IoT solutions contribute to substantial cost savings for metal fabricators.
4. Improved Product Quality
IoT sensors continuously monitor production parameters, ensuring consistent quality and reducing defects. Any deviation is detected early, preventing costly rework.
5. Better Workforce Safety
Smart sensors can detect hazardous conditions, such as excessive heat, vibration, or gas leaks, ensuring a safer working environment for employees.
Key IoT Applications in Metal Fabrication
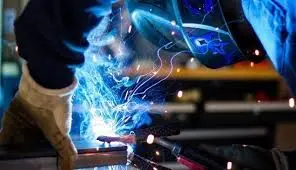
1. Predictive Maintenance
Traditional maintenance methods are reactive, leading to costly repairs and unexpected downtime. IoT-enabled predictive maintenance uses real-time data to assess machine health and schedule maintenance only when necessary.
2. Remote Monitoring and Control
IoT allows manufacturers to monitor and control machines remotely, providing real-time insights into production processes. This capability is especially useful for large-scale operations and multi-location facilities.
3. Smart Inventory Management
RFID tags and IoT sensors track raw materials, finished products, and tool usage, ensuring optimal inventory levels and reducing waste.
4. Energy Management
IoT-powered energy monitoring systems analyze power consumption patterns, helping manufacturers reduce energy waste and lower operational costs.
5. Automated Quality Inspection
Computer vision and AI-integrated IoT systems can inspect welds, cuts, and finishes with unparalleled accuracy, ensuring high-quality products with minimal human intervention.
6. Real-time Data Analytics
IoT sensors collect vast amounts of data that can be analyzed to detect trends, optimize production cycles, and improve decision-making processes.
7. Supply Chain Optimization
IoT enhances supply chain visibility by tracking material movement, predicting demand fluctuations, and ensuring timely deliveries.
Challenges of Implementing IoT in Metal Fabrication

1. High Initial Investment
Implementing IoT solutions requires significant upfront costs, including hardware, software, and infrastructure upgrades.
2. Data Security Risks
Connected devices are vulnerable to cyber threats, making it essential to implement robust security measures.
3. Integration with Legacy Systems
Many metal fabrication plants use outdated machinery, making IoT integration a challenge. However, retrofitting solutions can bridge the gap.
4. Skill Gaps in Workforce
Employees need training to understand and leverage IoT systems effectively, requiring additional investment in skill development.
Future Trends in IoT for Metal Fabrication
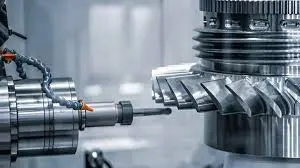
1. AI-Driven Analytics
AI will play a crucial role in analyzing IoT data, offering deeper predictive insights and process optimization.
2. Digital Twins
A digital twin is a virtual replica of a physical asset, allowing manufacturers to simulate and test processes before implementation.
3. 5G-Powered Connectivity
The rollout of 5G networks will enhance IoT connectivity, enabling faster data transmission and more reliable machine communication.
4. Blockchain for Secure Data Sharing
Blockchain technology can ensure secure and transparent data sharing across the metal fabrication ecosystem.
5. Advanced Robotics Integration
IoT-enabled robots will work alongside human operators, improving precision and efficiency in metal fabrication tasks.
Conclusion
The adoption of IoT in the metal fabrication industry is transforming traditional manufacturing processes, providing predictive insights that lead to smarter decision-making, improved efficiency, and significant cost savings. While challenges exist, the future holds immense potential for IoT-driven innovations. As technology continues to evolve, metal fabricators who embrace IoT will gain a competitive edge in an increasingly digital world.
FAQs
1. How does IoT improve predictive maintenance in metal fabrication?
IoT sensors continuously monitor equipment performance, identifying potential failures before they occur, reducing downtime and maintenance costs.
2. What are the main challenges of implementing IoT in metal fabrication?
Challenges include high initial investment, data security risks, integration with legacy systems, and workforce skill gaps.
3. Can IoT reduce material waste in metal fabrication?
Yes, IoT optimizes inventory management and monitors production processes to minimize material waste and improve efficiency.
4. What role does AI play in IoT-powered metal fabrication?
AI enhances data analytics, providing deeper insights into machine performance, production trends, and predictive maintenance.
5. Is IoT beneficial for small-scale metal fabrication businesses?
Absolutely. While initial costs may be high, IoT improves efficiency, reduces downtime, and enhances product quality, leading to long-term profitability.